The Science Behind Porosity: A Comprehensive Guide for Welders and Fabricators
Comprehending the intricate devices behind porosity in welding is critical for welders and fabricators making every effort for remarkable workmanship. From the composition of the base materials to the intricacies of the welding process itself, a wide variety of variables conspire to either worsen or relieve the presence of porosity.
Comprehending Porosity in Welding
FIRST SENTENCE:
Evaluation of porosity in welding discloses crucial insights into the integrity and top quality of the weld joint. Porosity, characterized by the existence of dental caries or gaps within the weld steel, is an usual concern in welding procedures. These gaps, otherwise appropriately addressed, can jeopardize the structural honesty and mechanical buildings of the weld, leading to possible failures in the ended up product.
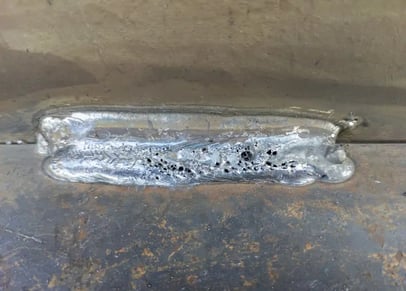
To identify and quantify porosity, non-destructive screening methods such as ultrasonic testing or X-ray examination are commonly used. These strategies enable the recognition of inner issues without jeopardizing the integrity of the weld. By analyzing the size, form, and distribution of porosity within a weld, welders can make educated choices to boost their welding processes and attain sounder weld joints.

Factors Affecting Porosity Development
The event of porosity in welding is influenced by a myriad of aspects, varying from gas securing effectiveness to the details of welding specification settings. Welding specifications, consisting of voltage, present, take a trip speed, and electrode kind, likewise influence porosity formation. The welding strategy utilized, such as gas metal arc welding (GMAW) or protected steel arc welding (SMAW), can influence porosity formation due to variants in warm circulation and gas coverage - What is Porosity.
Impacts of Porosity on Weld Quality
The existence of porosity also damages the weld's resistance to corrosion, as the caught air or gases within the gaps can respond with the surrounding atmosphere, leading to deterioration over time. Furthermore, porosity can prevent the weld's capability to endure pressure or influence, additional jeopardizing the total high quality and dependability of the bonded framework. In crucial applications such as aerospace, automobile, or structural buildings, where safety and security and sturdiness are vital, the destructive effects of porosity on weld top quality can have about his severe repercussions, stressing the significance of minimizing porosity via proper welding methods and procedures.
Strategies to Decrease Porosity
In addition, making use of the proper welding criteria, such as the right voltage, existing, and travel speed, is important in protecting against porosity. Keeping a consistent arc length and angle throughout welding also helps lower the possibility of porosity.

Moreover, selecting the right securing gas and maintaining correct gas circulation prices are crucial in decreasing porosity. Utilizing the suitable welding technique, such as back-stepping or using a weaving movement, can additionally assist disperse warmth evenly and lower the opportunities of porosity formation. Last but not least, ensuring proper air flow in the welding atmosphere to find more info eliminate any potential resources of contamination is essential for attaining porosity-free welds. By implementing these methods, welders can successfully lessen porosity and create top quality bonded joints.

Advanced Solutions for Porosity Control
Applying innovative modern technologies and cutting-edge approaches plays an essential duty in achieving remarkable control over porosity in welding procedures. Furthermore, employing sophisticated welding methods such as pulsed MIG welding or modified atmosphere welding can likewise aid minimize porosity concerns.
Another sophisticated remedy entails using sophisticated welding tools. As an example, utilizing tools with integrated functions like waveform control and innovative power resources can boost weld top quality and decrease porosity dangers. The application of automated welding systems with accurate control over parameters can significantly decrease porosity defects.
In addition, including innovative surveillance and evaluation technologies such as real-time X-ray imaging or automated ultrasonic screening can aid in detecting porosity early in the welding process, permitting for prompt corrective actions. In general, incorporating these innovative options can greatly boost porosity control and boost the overall quality of welded parts.
Conclusion
To conclude, recognizing the scientific research behind porosity in welding is vital for welders and producers to create premium welds. By identifying the factors influencing porosity formation and applying techniques to lessen it, welders can improve the total weld high quality. Advanced services for porosity control can better enhance the welding process and make certain a strong and blog trusted weld. It is very important for welders to constantly educate themselves on porosity and execute finest methods to accomplish optimum results.